ミニセミナー・基礎講座
コーティング
目次
塗布・乾燥プロセス
スピンコート法による膜質は均一である
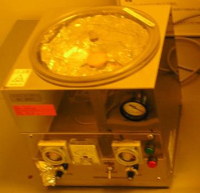
スピンコート法は、その均一性、プロセス、装置の簡易さにより多くの産業で用いられている。液晶や半導体デバイスにおいて、フォト高分子膜のコーティングや現像時のスピン乾燥に用いられている。右図はスピンコート装置の外観写真を示している。膜厚均一性を向上にはスピン乾燥が効果的だが、そのためウェハ周辺部の周速度は速くなり、高分子膜からの溶剤蒸発が不均一となる。高分子材料(レジスト)は、ノボラック樹脂 (m-クレゾール、p-クレゾール)、感光剤 (ナフトキノンジアジド)、溶剤 (エチルセルソルブアセテート) の混合物である。残留溶剤の絶対量は、高分子膜の重量変化として求める。また、スピン乾燥と高分子膜質との関係を調べるため、接触角や屈折率などを用いて解析する。純水の接触角は、高分子膜上に滴下して1分後の値を測定する。下の左図は高分子膜のウェハ半径方向の屈折率分布を示している。スピンコート後の高分子膜では、ウェハエッジに近づくにつれて屈折率がわずかに増加する。これは高分子膜質がウェハ面内で異なることを意味している。また、下の右図は高分子膜中の残留溶媒量を0~11mgの範囲で変化させた時の高分子膜の屈折率変化を示している。高分子膜中の残留溶媒量が減少するにつれて屈折率は増加する。よって下の左図のスピンコート後の高分子膜において、ウェハ周辺部は中央部に比べ溶剤が多く蒸発することが説明できる。これはスピンコート時の周速がウェハ周辺部の方が速く、溶剤の乾燥が促進されるためである。
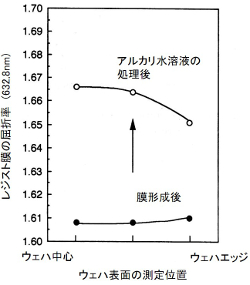
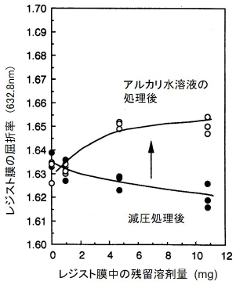
下の左図はスピン乾燥した高分子膜表面において、純水接触角のウェハ半径方向分布を示している。接触角はウェハエッジに近づくにつれ高くなり、また逆にスピンコート回転数の増加に従い低くなる。この結果は上の左図の高分子膜の屈折率分布と同様に、ウェハ面内での高分子膜の残留溶剤量の変化を表している。また、下の右図は、高分子膜内の残留溶剤量と純水接触角との関係を示している。残留溶媒量の減少とともに純水接触角は増加するため、接触角変化は高分子膜の外周部での残留溶媒量の減少を表している。この結果は下の左図の高分子膜内の屈折率分布と一致する。以上のように、高分子膜内の残留溶剤量は、スピン乾燥プロセスに大きく依存する。また、屈折率や接触角測定といった簡単な方法で塗膜の乾燥を解析できることも特長の一つである。
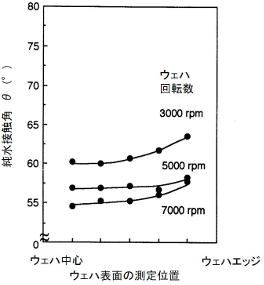
純水接触角のウェハ半径方向分布
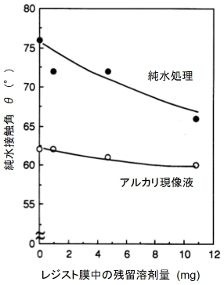
接触角との関係
ここでは、代表的な塗膜の乾燥装置について、装置機構および特徴について述べた。試料の大型化だけでなく、高品位な乾燥プロセスの要求が高くなり、乾燥装置の絶え間ない進展がみられる。塗膜の高品質化には、塗膜の性質に適した乾燥装置の選択が重要となる。
参考文献
- Akira Kawai, "Characteristics of Adhesion between Photoresist and Inorganic Substrate", Jpn. J. Appl. Phys. 28, 2137-2141 (1989).
- Akira Kawai, "Adhesion of Resist Micropatterns during Drying after Water Rinse", Jpn. J. Appl. Phys., 34, L1093-L1094 (1995).
- 河合 晃, "フォトレジスト膜の残留歪みと接着性に及ぼす溶剤の効果", 日本接着学会誌, 31, 187-191 (1995).
塗膜の乾燥による硬化メカニズムを明確にする
塗膜の乾燥プロセスは、塗工液から塗膜形成に至るダイナミックな形態変化といえる。塗工液中の溶剤は、均一でスムーズなコーティングにおいて重要な役割をする。乾燥プロセスは、塗膜内の溶剤の拡散現象が本質であり、乾燥装置の設計指針に大きく関与する。また、乾燥後の塗膜の凝集力発現には、溶剤の液体メニスカスによるラプラス力が寄与している。そして、熱処理により塗膜の凝集性はさらに向上する。ここでは、塗膜の乾燥プロセスに注目し、溶剤の拡散モデル、乾燥中のエネルギー収支、ラプラス力および熱処理による凝集力制御について述べる。
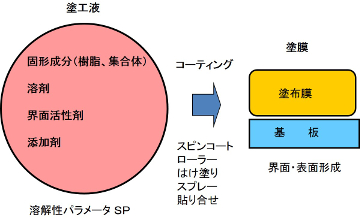
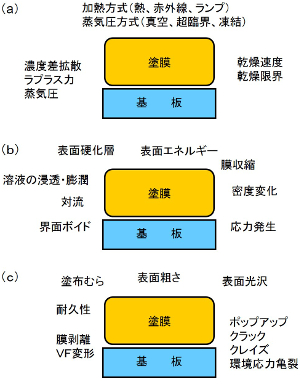
まず、塗膜の形成過程について概説する。上図のように、塗工液は、樹脂や高分子集合体からなる固形分と、溶剤および界面活性剤からなる液体との混合体である。よって、塗工液はコーティング性が高く、様々な表面形状の基材に塗布できる。また、溶剤量により粘度を決定し、界面活性剤によって濡れ性を繊細に制御できる。一方、塗膜形成によって、基板との界面が新たに生じる。この界面形成により、塗膜は強固な膜として安定化する。塗膜の形成過程には、様々な物理要因が関与する。右図(a)は塗膜の乾燥方法をまとめている。塗膜の乾燥要因は、溶剤の膜内拡散、固形分に働くラプラス力、膜内の応力発生などがある。乾燥方法は加熱方式と蒸気圧方式とに分かれる。加熱方式には、熱、赤外線、ランプ方式などがあり、蒸気圧方式には、真空、凍結乾燥、超臨界などがある。これらの乾燥プロセスにより、乾燥速度や乾燥限界が決められ、塗膜に様々な物性変化が生じる。乾燥後の塗膜のトラブル要因には、右図(b)のように、表面エネルギー、表面硬化層、膜収縮、界面ボイドなどの表面・界面的要因や、密度変化、応力発生、浸透膨潤などのバルク的要因がある。これらの要因が絡み合って塗膜の品質が決定される。塗膜の品質には、右図(c)表面光沢、塗布むらなどの視覚的な評価や、膜剥離、クラックなどの膜破壊に関するものがある。塗膜と基板との界面不安定に起因するトラブルも多い。
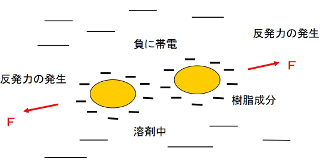
塗工液は、溶剤と固形分や添加剤の混合物であるが、上図のように、固形分はゼータ電位と呼ばれる特性電位を有する。多くの固体材料は液中で負に帯電している。よって、塗工液内の固形分には斥力が働くため凝集性が低くなる。下表は液中の無機・有機材料のゼータ電位を示している。ゼータ電位は電気泳動法などで測定可能であり、ミリボルト単位の電位を示す。純水、機能水、酸アルカリ中では、ほとんどの固体がマイナスに帯電するため凝集は生じにくい。ここで、混合メカニズムを、自由エネルギーで議論する。一般に、混合の自由エネルギー変化は以下で表せる。
ΔGm = ΔHm - T ΔSm
ここで、ΔGm:混合による自由エネルギー変化、ΔHm:混合による熱量変化(エンタルピー項)、T:絶対温度、 ΔSm:混合のエントロピー変化を表す。ここで、ΔGm<0であれば自発的な混合が可能となるため、Tの上昇、ΔHmの減少、ΔSmの増加が効果的である。また、ΔGm>0であれば、この系は溶解しにくく相分離が生じることとなる。
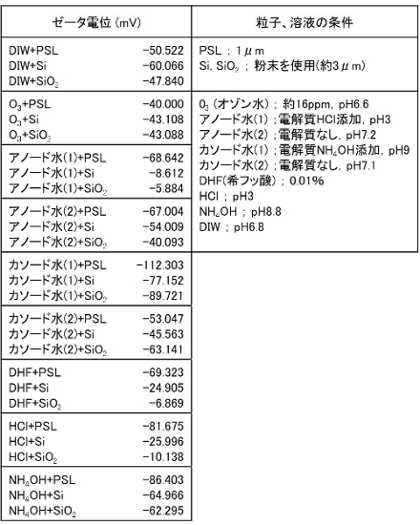
一方、溶解について以下のように解釈できる。一般に、帯電したイオン間に働く相互作用は、クーロン力Fとして表せる。
ここで、q1、q2はそれぞれ帯電電荷量であり、ε はイオンが存在する場の誘電率である。rはイオン間の最近接距離である。ここで、水中の比誘電率 ε は、大気中に比べて約80倍に増大するため、下図に示すように、イオン間の相互作用が低下し遊離する。また、溶解性パラメータ(SP) δ値も、溶解性の評価に用いられる。
δ = ( ΔE / V )1/2
ここで、ΔE:モル蒸発エネルギー(cal / mol)、V:モル体積 (cc / mol )、ΔE/V: 凝集エネルギー密度(cal / cc)である。すなわち、溶解のエンタルピーΔHSは以下のように表される。
ΔHS = Vm (δ1 - δ2 )2 φ1φ2
ここで、Vmは全体積、φ1とφ2は各体積分率を表す。ここで、
δ1 ≒ δ2
となることにより、ΔHSは最小となり溶解することとなる。
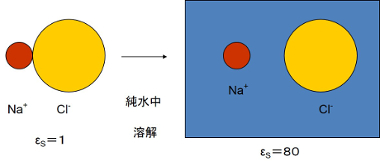
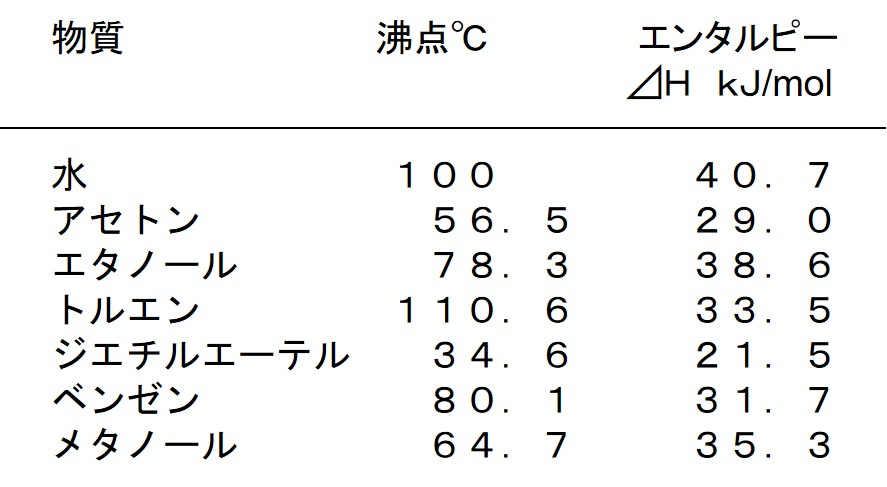
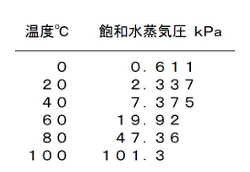
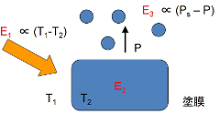
乾燥過程について、エネルギー収支に基づいてメカニズムを考察する。上の左表と右表は、各溶剤の蒸発エンタルピー、および、水の飽和蒸気圧の温度依存性を示している。溶剤の蒸発は、蒸発エンタルピーΔHが低いほど容易である。また、有機溶剤はエンタルピーが低く蒸発しやすいことが分かる。水の飽和蒸気圧は、環境温度が高いほど大きくなり、溶剤の蒸発が加速される。飽和蒸気の気体では、温度低下により凝縮し結露を生じる。よって、乾燥のしやすさも考慮して溶剤を選択する必要がある。ここで、乾燥プロセスにおけるエネルギー収支を考える。右図は、乾燥過程におけるエネルギー移動を表している。溶剤を含む塗膜の乾燥を行う場合、エネルギー保存則が成り立つため、周囲から塗膜に供給されるエネルギーE1は、塗膜の温度上昇のエネルギーE2と蒸発による消費エネルギーE3の和で表せる。ここで、T1は周囲の温度であり、乾燥装置内の温度に相当する。T2は塗膜の温度である。また、Pは塗膜内の溶剤の蒸気圧であり、PSは周囲の温度での飽和蒸気圧を表す。ここで、乾燥前は、温度差(T1-T2)が大きいため、供給熱エネルギーE1が大きくなる。しかし、塗膜はまだ低温であるため(PS-P)が小さく乾燥は始まらない。このプロセス初期の期間は、消費エネルギーE3が小さいため、乾燥は殆ど起こらず、塗膜の温度上昇Tが生じる。塗膜の温度上昇により温度差(T1-T2)が小さくなるため、乾燥装置からの供給エネルギーE1が小さくなる。また、周囲の温度上昇に伴い、飽和蒸気圧PSも大きくなる。よって、蒸気圧差(PS-P)が大きくなり、蒸発に伴う消費エネルギーE3が増加する。この間、塗膜の温度上昇はなくなり、乾燥期間中の塗膜の温度は一定となる。やがて、残留溶剤量が少なくなると、供給エネルギーは試料の温度上昇に費やされる。
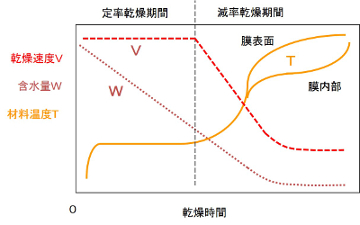
以上の考えに基づき、上図に、塗膜の乾燥プロセスおよび乾燥時間をまとめている。乾燥初期は塗膜の温度上昇に熱エネルギーが消費される。乾燥が始まれば塗膜の温度上昇は無くなり、一定の乾燥速度で乾燥する。最終段階で塗膜の温度が十分上昇すると、塗膜表面と内部の温度差が生じる。よって、耐熱性の低い塗膜を熱乾燥する場合は、乾燥が完了する前に加熱を停止し塗膜の温度上昇を防ぐ必要がある。
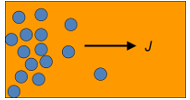
塗膜の乾燥モデルとして、塗膜内の溶剤の拡散現象に注目する。右図のように、塗膜表面から溶剤が蒸発することで、膜内の溶剤分布が不均一となる。そのため、溶剤の拡散は残留溶剤が均一になるように働く。一般に、拡散現象はFickの法則として表される。下式はFickの第1法則である。
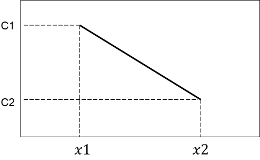
Jは拡散物質の流量、Dは拡散係数、Cは濃度、xは膜内の位置を表す。よって、拡散流量Jは、右図のように、濃度差と拡散係数に比例する。塗膜が飽和蒸気圧下にある場合、溶剤の蒸発は生じず、塗膜内の溶剤分布にも変化がない。よって、乾燥速度を高めるには、塗膜内の溶剤の濃度差を高くすることが効果的である。以下はFickの第2法則を示している。
上式では、拡散種濃度の位置xと時間t依存性を表している。下図(a),(b)には、拡散種が無限に存在する場合と、拡散種が有限の場合(通常乾燥に相当)における濃度曲線を示している。x=0において拡散種が無限にある場合、溶剤濃度は変化せず膜全体の溶剤濃度が上昇し均一となる。拡散種が有限の場合、x=0の濃度は減少するが離れた位置の濃度は増加し均一となる。通常の乾燥プロセスは後者である。よって、乾燥コントロールには、塗布膜内の残留溶剤の濃度と時間制御が重要となる。
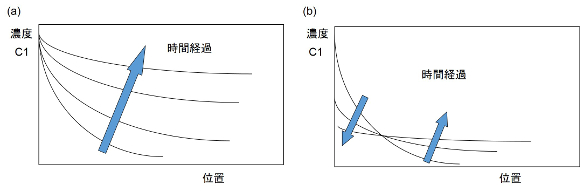
塗膜から溶剤が蒸発する過程で、下図のように、残留溶剤によりラプラス力が発生し膜内の凝集が始まる。ラプラス力の作用により、塗膜の凝集性が均一化される。凝集性の良質な塗膜を形成するために、ラプラス力は重要な働きをする。
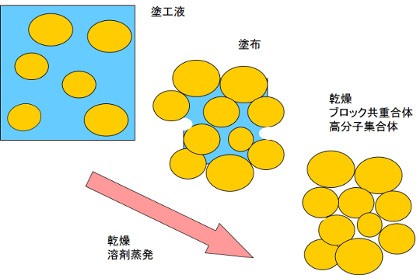
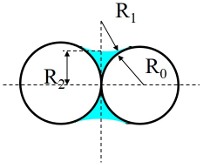
一般に、ラプラス力Fは、右図のような2つの球体の系において、以下のように定義される。
ここで、R1とR2はメニスカスの曲率半径である。γは液体の表面張力を表す。下図は乾燥後の微小球の凝集状態の拡大写真である。凝集により、直径の等しい微小球は、最密充填構造を構成する。また、サイズが異なる微小球では、小さい球が大きい球を囲むように配置する。このように、小さいサイズの固体ほど凝集性を支配することとなる。乾燥過程におけるラプラス力は、塗膜のミクロ構造形成に大きく影響する。
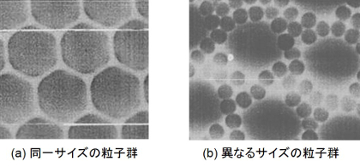
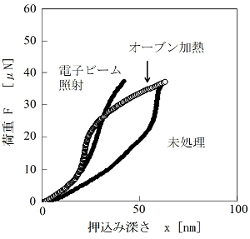
熱処理により塗膜内の残留溶剤が蒸発し、樹脂等の熱架橋反応が促進し凝集力が増加する。塗膜の凝集性の増加により、応力が発生するが耐久性も向上する。ここでは、塗膜表面の硬さ測定として、原子間力顕微鏡(atomic force microscope: AFM)を用いた押込み試験(インデンテーション)を紹介する。この手法は、微小プローブを塗膜表面から内部へ押込みながら荷重を計測し、硬さの深さ分布を計測する。右図は、力曲線として、塗膜表面層の硬化処理の違いを示している。熱処理法として、オーブン加熱、電子ビーム照射を用いている。表面から内部にプローブを押し込むにつれて、荷重が増加する様子が分かる。この場合、曲線の傾きが大きい場合は、比較的硬化が進んでいることを示す。結果として、熱処理によって、表面近傍は硬化しているが、必ずしも膜内は均一ではないことが分かる。これは熱伝導や溶剤の拡散状況などの違いに依存する。下図は塗膜表面に形成されたプローブの圧痕を示している。オーブン加熱と未処理の場合は、押込み深さは同じであるが、右図のように塗膜表面からの硬さ分布は異なる。
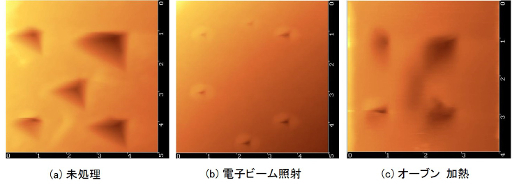
ここでは、塗膜の乾燥モデルとして、溶剤拡散、ラプラス力、熱処理による凝集性制御について紹介した。また、乾燥速度と乾燥時間、および乾燥時の試料温度制御について述べた。溶剤の乾燥に伴い、塗膜の凝集性が発現する。高精度で耐久性を有する塗膜形成には、バランスの取れた乾燥プロセスの選択が必要となる。
参考文献
- Akira Kawai, "Condensation of Nano-Size Polymer Aggregates by Spin Coating", J. Adhesion and Interface, vol.6 (1) 7-10 (2005).
- 河合 晃、"フォトレジスト膜の残留歪みと接着性に及ぼす溶剤の効果"、日本接着学会誌、31, 187-191 (1995).
- Akira Kawai, "Cohesion property of resist micro pattern analyzed by using atomic force microscope (AFM)", J. Photopolymer Sci. Technol, 16, 381-386 (2003).
- Akira Kawai, "Collapse Behavior of Micro Resist Pattern Analyzed by Tip Indentation Method with Atomic Force Microscope", J. Vac. Sci & Technol. B17, 1090-1093 (1999).
乾燥時の液体メニスカスの挙動を追う
塗膜の乾燥時の溶剤成分の液体メニスカスの存在により、凝集性が向上し塗膜形成に貢献する。乾燥時の液体メニスカスは、特定形状の微細構造を破壊することもある。微細加工(リソグラフィ)においては、頻繁に微細パターンが破壊され、しばしば問題化している。ここでは、パターン間に挟まれた液体メニスカスの乾燥過程を可視化し解析する。これにより、微細構造の液体メニスカスの乾燥過程が明らかになる。下の左図のように、2枚のPETパターン間に挟まれた液体メニスカスの乾燥挙動を解析する。まず、PETパターンを水槽内で純水に浸漬し、その後取り出して乾燥させる。パターン間に純水が残存するが徐々に乾燥する。下の右図は平行パターン間のメニスカスの乾燥過程を示している。最初はPETパターン間全体に純水が満たされている。乾燥が進むにつれて、パターン底部付近から乾燥が始まり、メニスカスが後退することで空気が入ってくる。両側のパターン底部から入った空気は中央で結合され、空気トンネルを形成する。空気トンネルにより純水は上部と下部に分離して残存する。さらに乾燥が進むと、パターン上部で純水は凝集し最後に消失する。パターン底部も同様に乾燥し消失する。このように、パターン間の空気トンネルの形成および乾燥は、パターン間に働くラプラス力と、パターン変形による間隔の変化に起因している。
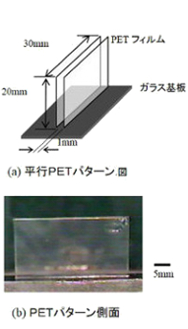
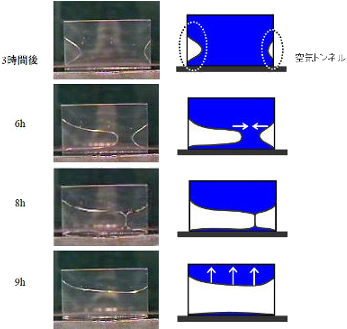
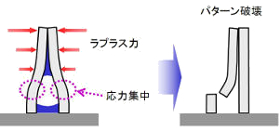
ここで、空気トンネル形成時の高分子パターン断面モデルを右図に示す。空気トンネルにより、パターン上部と下部の純水は分離される。そして、それぞれのメニスカス部においてラプラス力が働き、パターン底部では極端に応力が集中する。特に、高分子パターン底部は、S字状の変形を余儀なくされる。この時、高分子パターンと基板界面の付着力が低い場合は、パターン剥離が界面で生じる。パターン付着力が高い場合は、高分子パターンの凝集破壊が生じ、高分子残渣を生じて倒壊する。このような微細構造の破壊を防ぐには、液体メニスカスにより発生する応力の緩和およびパターン材料の凝集性の増大が効果的である。
参考文献
- Akira Kawai, J. Photopolymer Sci. Technol, 16, 381-386 (2003).
超臨界と凍結乾燥法によるラプラス力低減
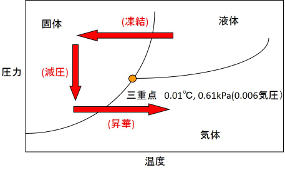
乾燥装置には、圧力や温度を制御し、過熱やラプラス力による塗膜の劣化を抑える方式も実用化されている。塗膜中の溶剤が蒸発する際、上述のように塗膜中に歪みが生じる。凍結乾燥方法は、溶剤の凝固点まで冷却し、その後、減圧中で溶剤を昇華させる手法である。右図のように、凝固点を迂回するように圧力と温度条件を設定する。減圧下での温度上昇により、固化した溶剤は膜外へ気体となって排出される。水溶性の塗膜の場合は、氷から直接水蒸気に昇華して乾燥が進む。よって、乾燥時には溶剤のラプラス力による塗膜の構造破壊が生じない。
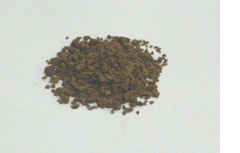
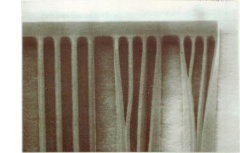
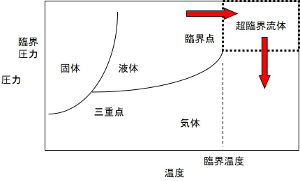
しかし、溶剤が昇華により抜けるため、塗膜内にはポーラスな微細構造が形成される。この乾燥方法は粉体形成に有効であり、上の左図のような食品分野で多く実用化されている。また、加熱乾燥や減圧乾燥では、上の右図のように、ラプラス力により微細パターンが変形する。このように、液体メニスカスにより微細構造が破壊される。しかし、超臨界乾燥ではラプラス力の作用を無くせるため、乾燥後の塗膜や微細構造に悪影響を及ぼさない。超臨界状態とは、右図にあるように、臨界点を超えた状態であり、液体と気体の区別が無いため表面張力が働かない。このような物質を超臨界流体と呼ぶ。下の左表には、二酸化炭素とエタノールの臨界点を示している。特に、二酸化炭素の臨界点は31℃、73気圧であるため、室温程度で処理可能となり装置も小型となる。下の右図には、炭酸ガスを用いた超臨界乾燥装置の外観写真を示している。水溶性の塗膜の場合は、事前にメタノールに置換してから、炭酸ガスの雰囲気で超臨界乾燥を行う。
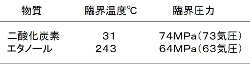
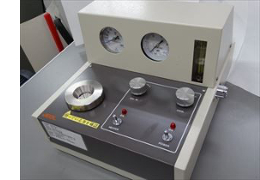
スピンコート法による膜厚10nm以下の自己組織化(SAN)膜の作成
一般的に膜厚10nm以下のキャスト法で形成した超薄膜には,不連続な網目状パターンが現れることが知られており,自己組織化ネットワークパターン(self-assembled network : SAN)構造と呼ばれている(下図)。多くの研究が行われてきたが,シングルナノリソグラフィにおいては,SAN構造を克服して連続的な超薄膜の形成が重要である。ここでは、フォトレジスト膜および低凝集力のフッ素系高分子材料(Nafion)のSAN構造に注目して解析を行った。
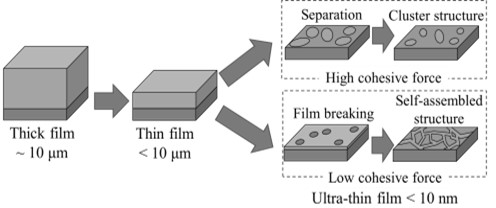
実験として,i線用ノボラック系ポジ型フォトレジストおよびパーフルオロスルホン酸(PFSA)を使用した。下表に実験フローを示す。SAN構造は,5000rpmでのスピンコート法によって形成した。さらに,原子間力顕微鏡(AFM)を用いてSAN構造を観察した。また,AFMを用いてレジスト厚膜の表面の形成された硬化層を解析した。
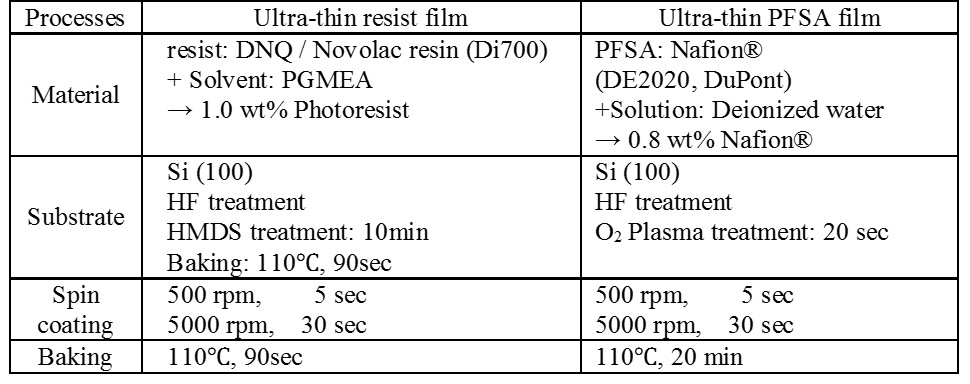
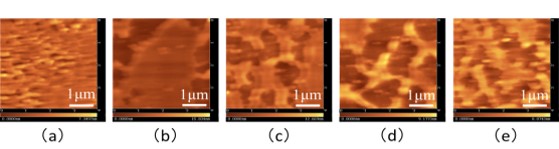
上図と下図のように,レジストとPFSAのSAN構造が明確に観察できる。SAN構造はウェハエッジ方向に連続的に変化している。下図のように,基板の回転中心から離れるに従って剪断力が大きくなるため,薄膜化しながらウェハエッジ方向へと延びていく。そして,この剪断力が連続膜としての凝集限界を上回ることで膜が破れSAN構造の形成に至ると考える。
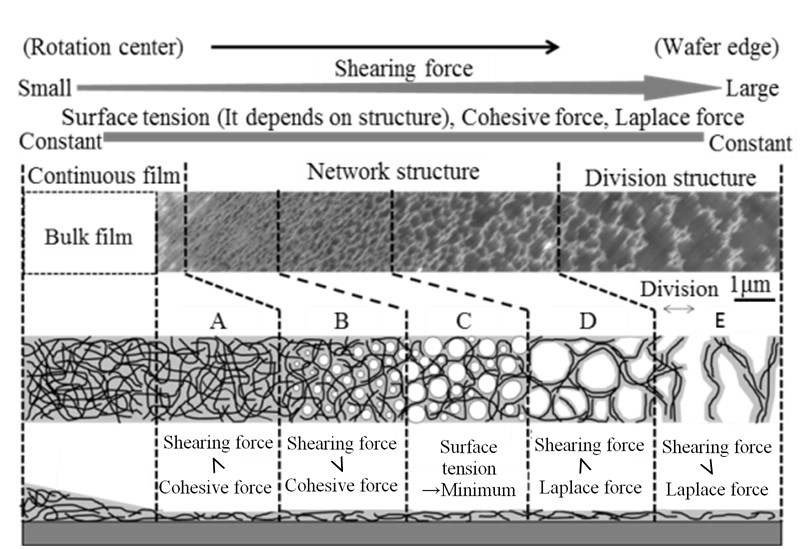
次に,下図はAFMによるレジスト厚膜の深さ方向での押込み荷重と硬さ曲線を示す。膜厚353nmのレジスト厚膜に対して,10nm以下の極薄い表面層では,相対的に硬化層が確認できる。
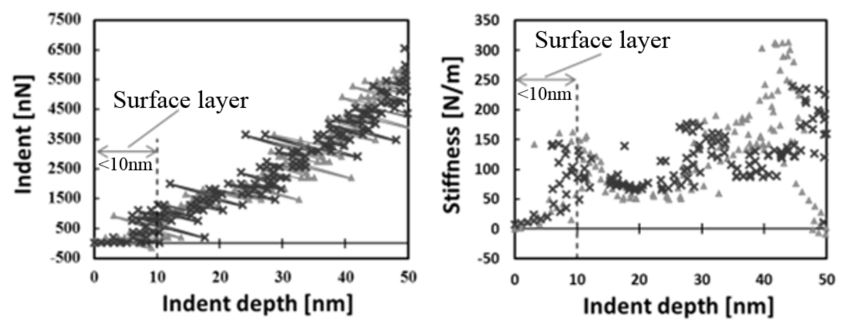
このことから,下図のモデルのように膜厚が薄くなるに従い,軟化層の割合が減少し,10nm以下の超薄膜では,表面硬化層が支配的になるものと考える。よって,10nm以下の超薄膜においては,スピン乾燥時の硬化層形成が支配的になることによりSAN構造が形成されると考えられる。
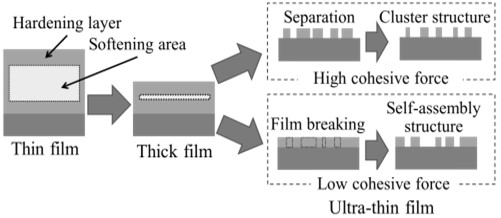
スピンコート法によって,レジスト膜とPFSA膜にSAN構造が形成されることを示した。また,レジスト膜には10nmの極表面層に硬化層が形成されることから,SAN構造はスピン乾燥時の硬化層形成が支配的であると考察した。
微粒子制御
小さいサイズの微粒子ほど凝集を支配する
同一サイズの微粒子は容易に最密充填構造をとる。これは凝集構造における表面積が最小となり、自由エネルギーの観点から安定となるためである。また、微粒子サイズの縮小に伴い微粒子間の吸着力も低下する。では、サイズの異なる微粒子群の凝集の場合では、どうなるのであろうか?
下の左図は5μmと1μmの粒径からなる微粒子群を懸濁液中で混合し乾燥させた場合の表面観察像である。大きい粒子は規則正しく最密充填の位置に配列しているが、その周囲に小さい粒子が密に凝集している。サイズの小さい微粒子の相互作用力は低いはずであるが、どのように説明すればよいのであろうか。2個の微粒子間の吸着力は幾何平均で表せる。これを下の右図のような1つの微粒子に隣接したn個の微粒子モデルに適用すると、その合力Fは以下のように表せる。
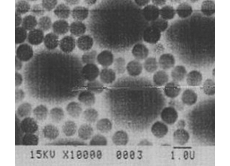
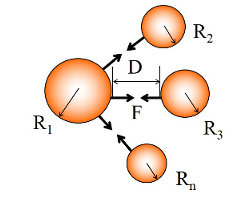
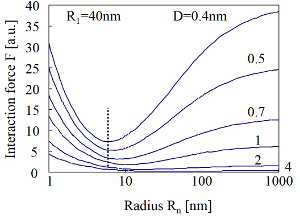
ここでdは微粒子間距離D0とD1との比である。すると、右図のように、相互作用する粒子サイズが減少しても、隣接する粒子数が増加するために、結果的に微粒子間の合力は増大する。よって、上の左図の観察写真のような凝集形態が得られる理由が理解できる。このような凝集構造の形成には、乾燥過程において微粒子間に存在する液体が大きい役割をする。安定構造を得るように、微粒子間の液体はメニスカス力によって各微粒子を強力に引き付ける。実際の微粒子の凝集系では、サイズおよび形状も異なるため、さらに複雑となる。しかし、サイズの小さい多数の微粒子が凝集形態を支配することに変わりはない。
参考文献
- 河合 晃, "AFM探針とポリスチレンラテックス(直径42nm~1μm)凝集粒子間の付着力解析 -DMT理論に基づく微粒子系の相互作用力の補正式-", 日本表面科学会誌, 19, 491-497 (1998).
- Akira Kawai, "Condensation of Nano-Size Polymer Aggregates by Spin Drying", J. Adhesion and Interface, vol.6 (1) 7-10 (2005).
微粒子の凝集はサイズに依存する
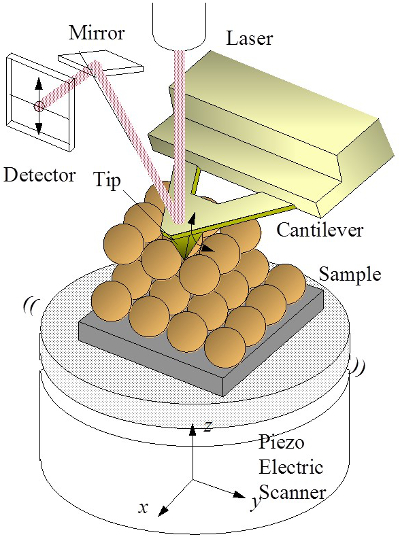
微粒子を主原料とするトナーインクや顔料などの分野では,これらの凝集性や付着挙動の解析が重要になる。また、太陽電池パネルやリチウムイオン電池においては、金属ナノペーストを材料とした金属配線形成技術が実用化されている。さらに、電子デバイス製造における洗浄プロセスや微細加工プロセスでは、基板上のナノ粒子の除去技術が重要になっている。このように、微粒子の実用範囲は拡大しているが、その凝集状態の物性はどのように解析できるのだろうか?
ここでは、原子間力顕微鏡(AFM)を用いて、微細探針と微粒子間の吸着力を測定し、さらに、微粒子凝集表面にスクラッチング試験による破壊挙動を紹介する。具体的には、粒径が42~1000nmの範囲のポリスチレンラテックス(PSL)の凝集性を、右図のようにAFMを用いて解析する。AFMのプローブ探針の先端曲率半径は8nm以下である。AFMを用いると、下図のような規則的な最密充填構造を観察できる。
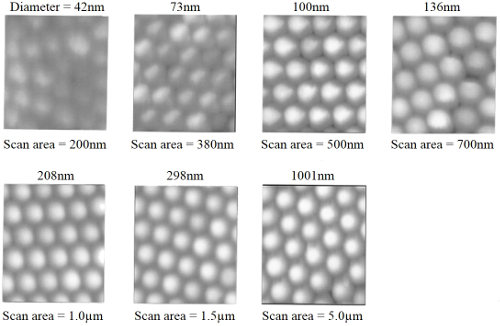
微粒子間は点接触ではなく変形しており有限の接触面積を有している。この変形は微粒子間の相互作用力に基づいて生じている。JKR理論によれば、変形面の半径aは、次式で表される。
ここで、WAは熱力学的な接着仕事、Rは粒子半径、Kは体積弾性率を表す。また、γはPSLの表面自由エネルギーである。さらに、PSL凝集表面にAFM探針を接触させて相互作用力を測定する。下図のように、AFM探針の吸着力はPSL微粒子の半径の減少に従い減少する。一般に、2つの球の半径を、それぞれ、R1とR2とした場合、相互作用力(吸着力)は幾何平均により表される。
ここで、HはHamaker定数を表し、D0は球間の距離を表す。実際の吸着力データは、PSL微粒子の半径が1μm以下になると幾何平均曲線から外れている。これは、微粒子の変形によって、相互作用力の働く有効面積が拡がるためである。よって、下図の場合、PSL微粒子の有効曲率半径が30%増加した場合の補正後の幾何平均曲線にほぼ一致する。
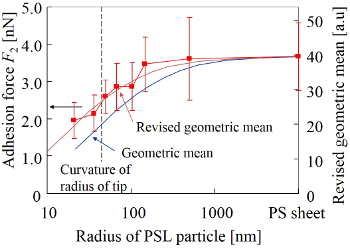
参考文献
- 河合 晃, "AFM探針とポリスチレンラテックス(直径42nm~1μm)凝集粒子間の付着力解析 -DMT理論に基づく微粒子系の相互作用力の補正式-", 日本表面科学会誌, 19, 491-497 (1998).
- Akira Kawai, "Condensation of Nano-Size Polymer Aggregates by Spin Drying", J. Adhesion and Interface, vol.6 (1) 7-10 (2005).
小さい微粒子の凝集力は下がる
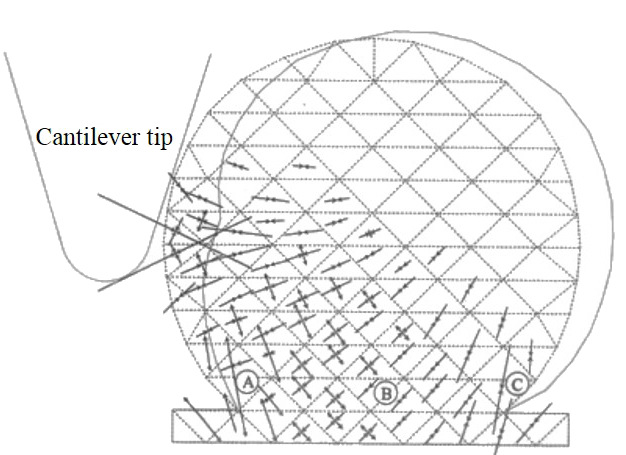
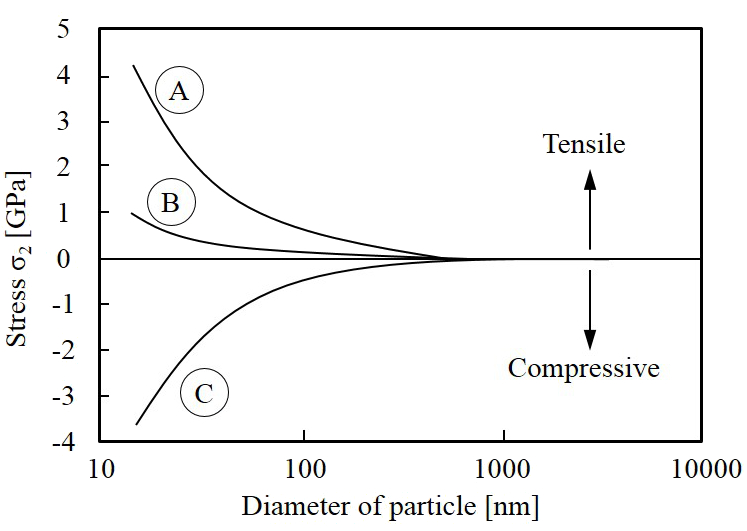
微細サイズの材料は、製品の機能性を十分に発揮するために重要な材料である。物質が微細サイズになると、その表面特性が支配的な物性になる。固体、液体、気体においても、微細サイズ特有の性質を有する。微粒子を主原料とするトナーインクや顔料などの技術分野においては,これらの凝集性や付着挙動の解析が重要になる。また、電子デバイス製造における洗浄プロセスや微細加工プロセスでは,粒径が50nm程度の微粒子の付着力制御が重要になってきている。しかしながら、現在のところ、固体基板上に付着した粒径50nm以下の微粒子は、光散乱法を原理としたパーテイクルカウンターを用いて検出することは困難である。このような微細サイズの特性解析には、原子間力顕微鏡(AFM)の使用が有効である。AFMを用いることにより、像観察だけでなく、凝集性や相互作用力の解析が可能となる。ここでは、ナノ粒子に対して、観察および凝集性の解析技術について述べる。右の上図は、AFM探針を用いてPSL球に荷重を加えたときの応力分布と変形図を示している。探針との接触点で、PSL球に10nmの変位が生じる横方向荷重を加えた場合、A点あるいはC点の界面近傍には、それぞれ引っ張りと圧縮応力が集中する。それに伴い基板上のPSL微粒子は変形している。右の下図は、これらの点で生じるPSL球内の応力の粒径依存性を示している。すなわち、粒径が約100nm以下になると基板との界面に集中する応力が急激に増加する。さらに、下図は、PSL微粒子の最密充填表面に対してAFM探針によるスクラッチ試験結果を示している。100nmの粒径ではスクラッチラインが明確に描画されることから、粒子間の付着力が高く、PSL粒子が塑性変形している。それに対し、73nmと42nmの粒径の場合は凝集表面が大きく掘れてしまう。この場合、PSL微粒子間の付着力が低下したことを示しており、吸着力と微粒子内応力が影響したと考えられる。このように、AFMを用いることで、微粒子の凝集挙動を直接解析できる。
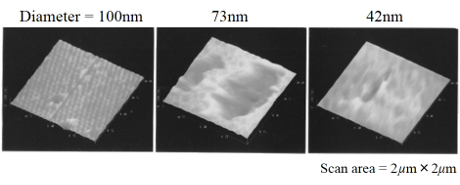
参考文献
- 河合 晃, "AFM探針とポリスチレンラテックス(直径42nm~1μm)凝集粒子間の付着力解析 -DMT理論に基づく微粒子系の相互作用力の補正式-", 日本表面科学会誌, 19, 491-497 (1998).
- Akira Kawai, "Condensation of Nano-Size Polymer Aggregates by Spin Drying", J. Adhesion and Interface, vol.6 (1) 7-10 (2005).
塗膜の性質
塗膜の表面には極薄い硬化層ができている
通常、塗工膜のコーティング後には熱処理を行うが、その膜の均一性はどうであろうか?これは、塗工膜内の残留溶剤の蒸発促進、塗膜の凝集性の向上、および基板との付着性の改善などが目的である。そして、熱処理後の塗膜には、表面硬化層が形成される。この表面硬化層の膜厚は20nm程度であり、原子間力顕微鏡(AFM: atomic force microscope )による微細探針のインデンテーション(押込み試験)解析によって検出できる。ここでは、スピンコート法で作製した高分子膜の硬さの深さ方向分布について述べる。特に、AFMを用いた高分子膜の表面硬化層の検出、およびその解析手法について述べる。
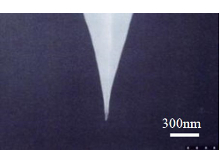
右図は、インデンテーション試験に使用される微細カンチレバー探針の先端写真を示している。先端の曲率半径は8nm、ばね定数は97N/mであり、高分子膜内へシャープな先端を押し込むことができる。下図はAFMの微細探針を用いたインデンテーション法の概略を説明している。最初に、高分子パターンの表面像をナノスケールで観察し、AFM探針をインデントする位置を決定する。その後、探針を高分子膜内へ荷重をかけて押し込みながら荷重曲線を取得する。インデンテーション試験は、(a)高分子パターン上面、(b)パターン側面、および、(c)パターン内部での試験が可能となる。パターン内部のインデンテーション試験では、あらかじめパターン表層部をAFM探針で除去し、パターン内部を露出させる。そして、露出させた高分子膜表面にAFM探針をインデントする。このような細かい操作もAFMを用いることにより可能となる。インデンテーション試験のサンプルは、アクリル系樹脂を主成分としたArF化学増幅型レジストを用いている。
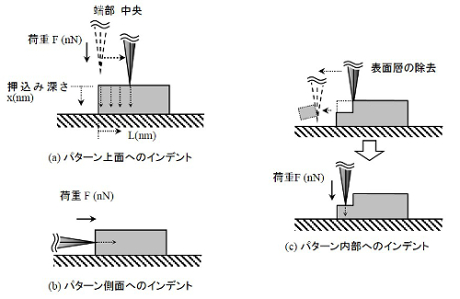
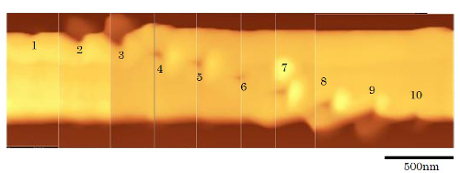
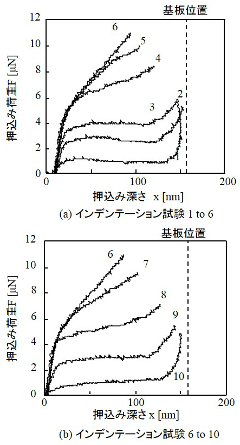
(各曲線の番号はインデント位置を示す)
上図は、インデンテーション試験後の線幅500nmの高分子パターン像である。インデンテーションの痕跡が明確に確認できる。ここでは、隣接するインデント試験同士が影響しないように、インデント位置を徐々にずらしている。よって、高分子パターンの横断面内の硬さ分布を解析できる。また、パターンエッジ付近では、AFM探針をインデントすることにより、パターン側面が崩れている。パターンエッジ部では、インデンテーション試験に誤差が含まれる。右図は、各インデント位置での荷重曲線を示している。パターンエッジ付近では、比較的低い荷重で探針がインデントされている。これは、パターンエッジ部での破壊に起因する。パターン中央付近では、良好な荷重曲線が得られており、パターンエッジ部の影響は無い。荷重曲線には、パターン表面で傾きが大きく、内部に進むにつれて低くなっている。これは、高分子膜表面の硬化層の存在を示しており、その膜厚は約20nmである。さらにAFM探針をインデントして基板近くでは、探針を押し込めなくなる。基板近傍でも硬化層が存在しており、これはホットプレートによる基板からの熱伝達に起因した硬化である。下の左図は、高分子パターン上面、側面、内部でのインデンテーション試験による荷重曲線の傾きを示している。荷重曲線の傾き(N/m)は、その深さ位置での押込み硬さを表す。高分子パターン上面には、内部に比べ大きい硬化層が存在する。パターン側面にも僅かな硬化層が形成されている。このように、同一の高分子パターン内でも凝集性に違いがあることが分かる。よって、下の右図にパターン断面における硬化層モデルを示している。パターンを覆うように表面硬化層が形成されている様子が分かり、乾燥プロセスに大きく起因している。また、高分子パターン側面の凝集性は、エッジラフネスとしてパターン寸法精度に直接影響する。以上のように、AFMを用いたインデンテーション試験によって、微細構造内の凝集性を定量的に得ることができる。
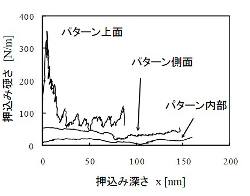
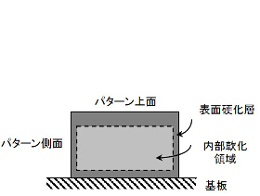
参考文献
- Akira Kawai, "Micro wetting system by controlling pinning and capillary forces., Microelectronic Engineering, 83, 1280-1283 (2006).
高分子膜の表面粗さをナノスケールで制御する
様々な機能性電子デバイス研究の基盤となるリソグラフィ技術において、微細ゲート電極作製のために、15nm幅の高精度な高分子パターン作製が必須の開発課題となっている。しかし、高分子パターン側面にはライエッジラフネス(LER)と呼ばれる5nm程度の凹凸が存在し、これがデバイス精度を低下させている。ここでは、LERの原因となるナノ高分子集合体の凝集メカニズムを明確にし、周期的な配列技術を実験的に構築する。また、原子間力顕微鏡(AFM)を用いて、高分子パターン内に存在する微細空孔(vacancy)の制御技術を構築し、高分子集合体の人工的な3次元構造の配列技術について述べる。
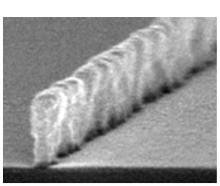
ナノエッジラフネス(LER)(60nm幅パターン)
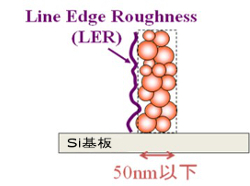
ナノラフネス形状
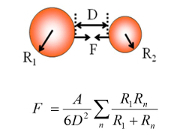
集合体間の相互作用解析
(Derjaguin近似モデル)
近年、高分子材料に代表されるように、ナノスケールでの高分子パターン形状の制御技術の重要性が増している。高分子材料は、化学増幅型としてのスチレン系、および汎用型のノボラック系樹脂をベースポリマーとして、超LSIやディスプレイデバイス等のリソグラフィのエッチング用加工材料として実用化されていている。しかしながら、上の左図および上の右図にあるように、高分子集合体の凝集挙動により、パターン形状全域に凹凸が生じている。これは、ラインエッジラフネス(LER)と呼ばれ、電子デバイスのゲートおよび配線パターンの加工精度の低下を招く。しかし、高分子パターンには様々な熱処理が施されるため、高分子集合体の凝集制御によって、ナノ制御システム創発への期待が高まってきている。河合研究室では、高分子パターン内に高分子集合体の欠落したナノ空間(vacancy)が存在することを実験的に見出した。また、右図のように、微小粒子モデルとして仮定した集合体間の相互作用は、それぞれ微小球サイズの幾何平均で表せる。ここでは、15nm以下の高分子パターンのLERを低減し、電子デバイス用の高精度なパターン形状を構築できる高分子パターンの凝集構造を考察する。具体的には、樹脂中の高分子集合体のナノスケールの物理的凝集過程を微小球モデルで検討し、実験的にLER形状の発現メカニズムを解析する。そして、下図のように、原子間力顕微鏡(AFM)を用いて、高分子集合体の凝集モデル化、高分子パターンの表面硬化層、高分子パターン内のナノ空孔であるvacancyについて述べる。
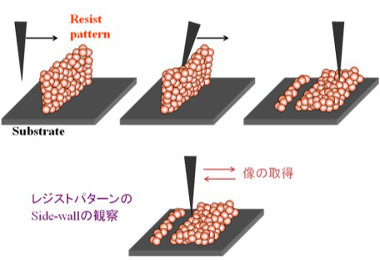
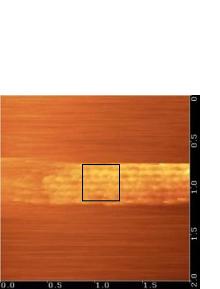
周期的なナノラフネス形状
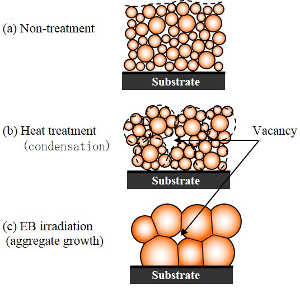
凝集モデルおよび空孔vacancyの発生機構
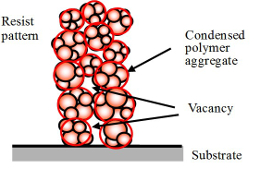
凝集構造モデルの構築
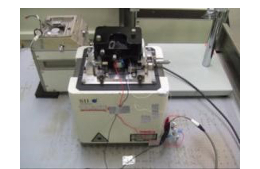
ナノパターンのLER制御
上の左図は、河合研究室で開発した「微細高分子パターンを基板から剥離し倒壊させる技術(DPAT法、Direct Peeling with AFM Tip)」を用いて測定したパターン側面の凝集形状を示している。パターン側面には、LERの原因となる約25nm程度の周期的凹凸構造が明確に観察できる。この周期構造は、様々なサイズを有する高分子集合体の熱的移動に従って生じると考えられる。実験的には、(1)熱処理による周期構造の成長挙動、(2)AFMによる表面硬化層の検出、(3)ナノ空孔(vacancy)の検出、(4)高分子集合体のマニピュレーションなどが可能である。これらより、高分子パターン表面のLERが表面エネルギーの支配によって、凝集の自由度が低下することが考えられる。これが上の右図のように立体構造になると、3次元的な凝集性が現れるとともに、高分子集合体の空孔(vacancy)を形成する。そして、右の上図のように、微小粒子モデルとして仮定した場合の高分子パターンの凝集モデルを検討し、15nmクラスの最適な凝集構造を構築できる。具体的には、右の下図にある原子間力顕微鏡(AFM)を用いて、このDPAT法により、高分子パターン側面の凝集形態をナノスケールで観察する。高分子パターン表面の硬化処理は、電子線(EB)照射システムを用いて実施する。そして、下図のように、側面の周期構造制御の可能性を確認できる。EB硬化処理により、高分子集合体が成長し、さらにLERが減少する条件を見出すことができる。
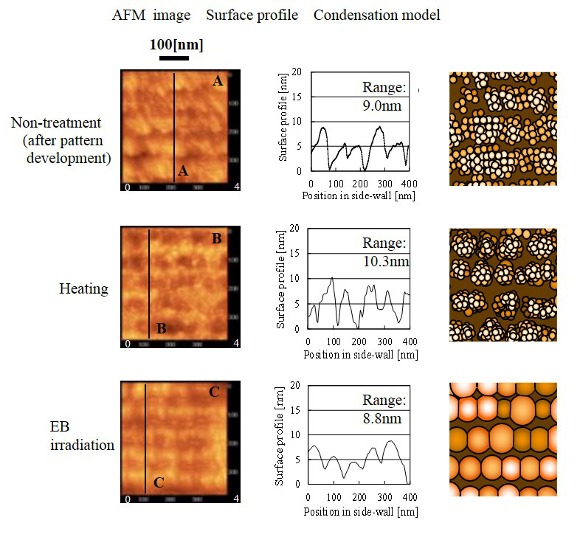
参考文献
- H. Ito, C.G. Willson, Polym. Eng. Sci. 23, 1012 (1983).
- A. Kawai, Microelectronic Engineering,83,659-662 (2006).
- A.Kawai.J. Photopolymer Science and Technology, 18(6), 729-736 (2005).
- A. Kawai, J. Adhesion and Interface, vol.6 (1) 7-10 (2005).
ナノマニピュレーション法による凝集性解析
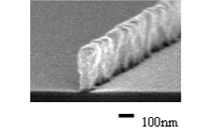
ラインパターンのSEM像
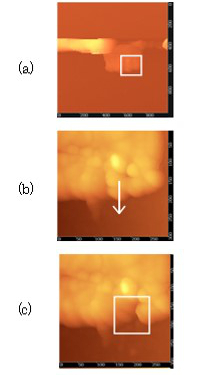
ナノマニピュレーション
高分子パターンのサイズが100nm以下になると、右の上図の高分子パターンに見られるように、20~30nmのサイズの高分子集合体に起因した表面凹凸が顕著になってくる。この表面凹凸は、微細加工の点からは、ラインエッジラフネス(LER)として加工寸法精度を低下させる。この表面凹凸は、高分子集合体と称する高分子の凝集単位により構成されている。高分子集合体の凝集挙動は、付着性などの機械的特性にも大きく影響を及ぼす。右の下図にはAFM探針を用いて、高分子パターンから高分子集合体を分離させた様子を示している。ここで(a)は、AFMの探針を用いて、ラインパターンの一部を剥離し倒壊させたAFM像である。(b)にあるように、倒壊したパターンの表面には、約30nmの高分子集合体が凝集している様子が分かる。そして、図中、矢印のように高分子集合体へ探針で荷重を加える。その結果、(c)にあるように、凝集している高分子集合体の一部を剥離し分離させることができている。このように、高分子集合体を分離させることで、パターン全体としての凝集性を解析することが可能である。下の左図は、さらに荷重を掛けることで、AFM探針を用いて分離した2個の高分子集合体を17個の微細な高分子集合体に分離している。よって、当初、2個と見られていた高分子集合体は、多数の小さい高分子集合体の凝集によって形成されていたことになる。このときの高分子集合体の分離に必要な荷重を下の右図にまとめた。高分子集合体の分離に必要な荷重は、3~8nN程度の非常に弱い力である。また、高分子集合体のサイズの縮小に伴い、分離力は減少することがわかる。よって、高分子集合体は有限の凝集力を有しており、凝集粒子のように取り扱うことができる。このように、AFM探針を用いたマニピュレーションにより、高分子パターンの凝集性をナノスケールで解析することが可能となる。
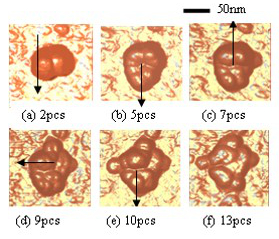
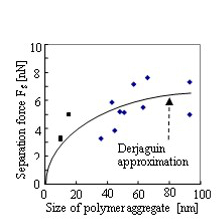
マニピュレーション荷重との関係
参考文献
- Akira Kawai, J. Photopolymer Science and Technology, 15, 371-376 (2002).
- Akira Kawai, J. Photopolymer Science and Technology, 16, 381-386 (2003).
アルカリ水溶液の浸透による応力変動
塗膜の付着不良は、基板との界面へ溶液が浸み込む事により起こる。一方、ポリマー内部への溶液の浸透現象を用いて、付着挙動を考察することは非常に興味深い。ここでは、高分子膜中への溶液の浸透量の変化と付着挙動について述べる。ここでは、同種の塗膜において、残留溶媒量をパラメータとして変化させている。ここで用いた高分子膜の溶媒はECA(エチルセルソルブアセテート)である。スピンコート法によって高分子膜を1.3μmの膜厚で基板上に形成した。この時の回転数は4500rpmである。基板としてSi(100)の6インチウェハ上に0.25μm膜厚で成膜された熱酸化膜を用いた。そして、高分子膜を90℃30分間0.1~760Torrの各真空度で熱処理を行なった。固形分の重量としては、0.1Torrで真空処理した後の高分子膜重量を用いた。(この時溶媒は完全に除去されたものと考えた)。そしてこの重量と各真空度で処理した膜の重量の差がそれらの膜中に残存する溶媒重量であるとした。高分子膜の膜厚はTencor社の表面粗さ計α-stepにて測定した。高分子膜の密度を、重量及び体積測定より求めた。HMDSのような密着強度処理は行っていない。縮小投影露光機を用いてミクロンサイズのパターンを高分子膜上へ焼き付けた。その後、TMAH水溶液中に20分間浸漬し、パターン現像を行った。現像後、一辺が0.5~100ミクロンの正方形パターンを用いて付着不良の確認を行った。同様に、0.5%HF水溶液中での付着強度も調べた。HF水溶液中で酸化膜基板はエッチングされ、アンダーカット形状を形成する。この様子をSEM(日立S-600)を用いて確認した。現像液の高分子膜表面に対する濡れ性の指標として濡れ仕事Wa(mJ/m2)を用いた。この時、現像液の表面エネルギーとして71.6mJ/m2を用いた。高分子膜内への現像液の浸透は、浸漬前後の高分子膜の電気抵抗を測定する事により確認した。下図にその測定方法を示した。2本のAl電極を備えた基板に高分子膜を塗布し、浸漬前後でその電極間の抵抗値の変化を調べた。現像液であるTMAH水溶液は強アルカリで良導体であり、高分子膜内へ浸透があれば高分子膜の抵抗値は下がると考えた。フォト高分子膜の内部応力を、Ionic社製の歪ゲージを用いて測定した。この計器でわずかな応力変化を検出する事ができる。
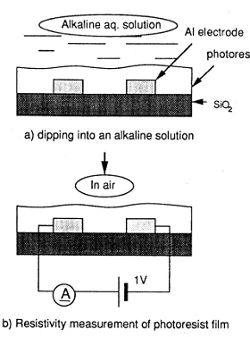
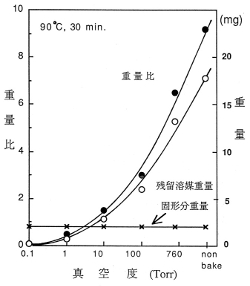
重量比の真空処理依存性
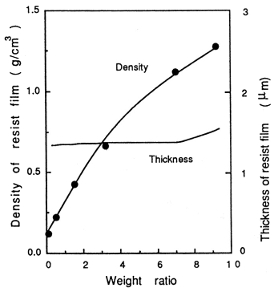
上の左図は各真空ベーク条件における高分子膜内の残存溶媒と固形分との重量比を示している。重量比は、残留溶媒量/固形分で表している。減圧していく事により溶媒の蒸発量は増し、結果として高分子膜の重量は減少している。0.1Torrの真空処理によって、残留溶媒量はほぼ0となっている。又、高分子膜コーティング直後の重量比は約10を示しているが、それは真空処理を行なう事により徐々に減少している。上の右図には各重量比における高分子膜の膜厚と密度を示している。溶媒が蒸発していくにつれ密度は減少し、膜厚もわずかながら減少していく。この事より高分子膜から溶媒が蒸発した際、固形分はその三次元的な構造を変化させないと考えられる。すなわち、溶媒がなくなった分だけポーラスな構造になっている可能性がある。これらの溶媒蒸発メカニズムを下図(a)~(b)にモデルで示している。
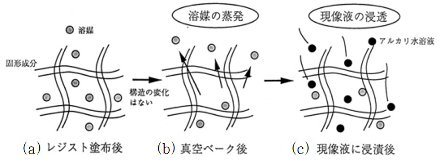
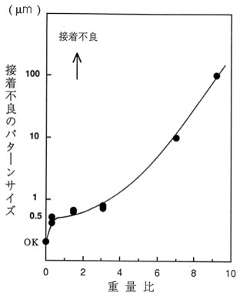
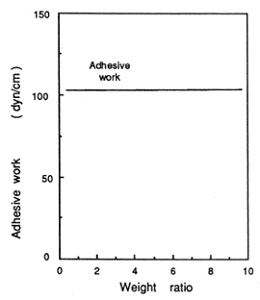
上の左図には、以上の真空処理を行なった各高分子膜の現像液中での付着強度を示している。縦軸には現像液に浸漬後に酸化膜基板上に残っていた高分子膜パターンのサイズを示している。残存パターンサイズが小さい程、付着強度は高いと言える。図より、残留溶媒量が減少するに従い付着強度は増加している事がわかる。残留溶媒量が0になった場合に、付着強度は最も高い値を示している。上の右図は、高分子膜上でのTMAH現像液の濡れ仕事Wの残留溶媒量依存性を示している。本実験においては各高分子膜に対する現像液の濡れ性に殆ど差が見られていない。よって表面エネルギー理論から推定される付着の挙動は、残留溶媒によらず同一となり、上の左図の実験結果とは矛盾することになる。よって、他のモデルが必要となる。
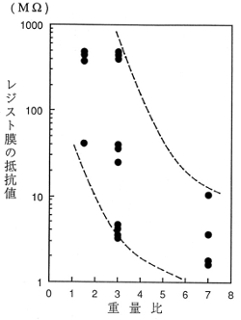
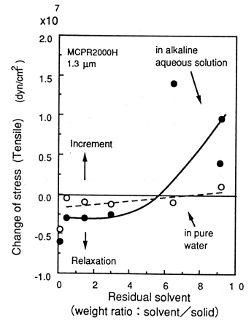
上の左図は、TMAH現像液に浸漬後の高分子膜の抵抗値を示した。残留溶媒量の増加に伴い、抵抗値の減少が見られている。よって、溶液の高分子膜への浸透が残留溶媒の存在により加速されたと言える。これは、図1(c)に示した様に、固形分の間に溶媒が存在していると、TMAH現像液は溶媒との相互作用(拡散、濡れ)によって膜内部への浸透が加速されるためと考えられる。逆に、溶媒が蒸発していくと固形分はポーラスな構造をとるため、TMAH現像液は膜内へ拡散しにくくなる。よって、上の左図の抵抗値の残留溶媒量依存性が説明できる。上の右図には、各残留溶媒量の高分子膜を、TMAH現像液及び純水に浸漬した場合の内部応力変化を示している。TMAH現像液に浸漬した場合、高分子膜の残留溶媒量が増加する事によってストレス量は増加していく。これは、残留溶媒によって浸透が加速されたTMAH現像液と高分子膜固形分(クレゾールノボラック)との反応、たとえばクロスリンクが原因で生じると考えられる。下の左図には以上の効果をモデル化している。この反応は、純水に浸漬した場合にストレス変化が殆ど見られない事よりも確かめられる。純水とポリマーとの反応性は非常に低い。この高分子膜の内部応力の増加は、高分子膜と基板との結合力を弱め界面に現像液の侵入を加速させる働きをする。下の右図には、以上の高分子膜を用いて酸化膜基板をHF溶液でエッチングした際のアンダーカット形状を示している。残留溶媒量の増加によりアンダーカット量は増加する傾向にある。同様に、HF溶液中においても高分子膜膜の内部応力が原因で付着力が減少すると考えられる。
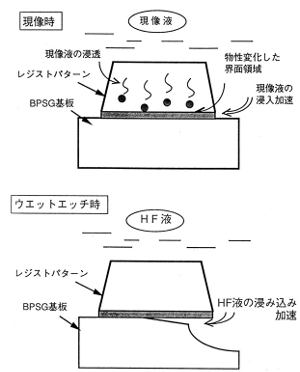
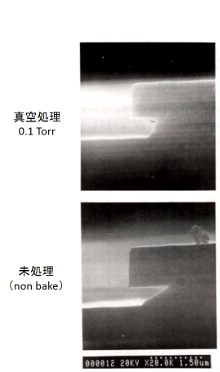
ここでは、フォト高分子膜内へのアルカリ現像液の浸透と、現像液中での付着強度について考察した。ここでは2つの注目すべき現象が分かった。1つは高分子膜の残留溶媒量が多いと溶液の浸透が加速されるという事である。2つ目は、その溶液の浸透により高分子膜の内部応力が増加するという事である。付着の新たなモデルとして、現像液の高分子膜膜内への浸透、膜の内部応力の増加、付着力低下に至ると言える。
参考文献
- Akira Kawai, "Characteristics of Adhesion between Photoresist and Inorganic Substrate" , Jpn. J. Appl. Phys. 28, 2137-2141 (1989).
- 河合 晃、"フォト高分子膜膜へのアルカリ水溶液の浸透と付着性"、日本付着学会誌、32, 294-297 (1996).
熱処理により界面への溶液浸透は加速する
塗膜に熱処理を行った場合の界面歪みについて、HFウェットエッチングを用いたアンダーカット法で解析する。下図(a)~(d)にHF水溶液でエッチングしたSiO2基板のアンダーカット形状を示している。(a)は、線幅2μmのパターンである。遠紫外線(DUV)硬化処理は行っていない。アンダーカット形状は異方性を示し、エッチング初期に等方性であったことが確認できる。(c)は2μm線幅のパターンにDUV照射を行った場合である。等方的なアンダーカット形状が増えて、2段形状を形成している。(b)は、幅広いパターン(15μm)にDUV照射を行った場合である。等方的な領域が(c)に比べて減少し、界面へのしみ込みが増加している。(d)は2μm線幅であり、DUV照射を受けた後に220℃でハードベークしたパターンである。等方的な形状はまったく見られない。また、(c)に比べてアンダーカット量は約1.5倍に増加している。すなわち、接着強度が低下している。
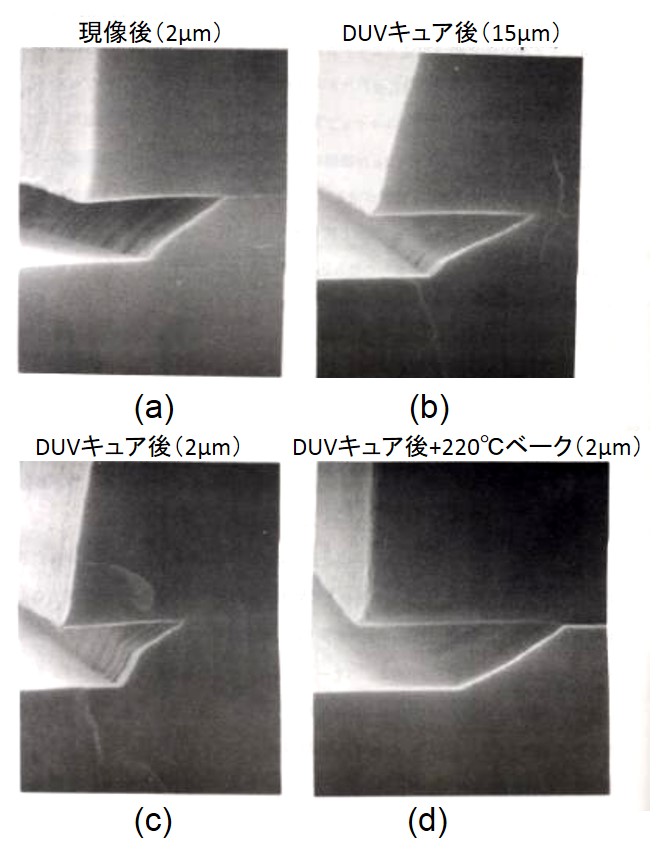
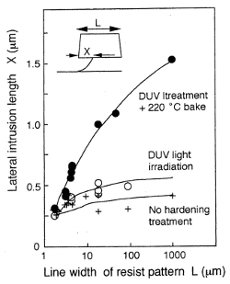
右図にアンダーカット量のパターン線幅依存性を示している。線幅の増加と共にアンダーカット量は増加し、やがて飽和している。DUV照射、及びハードベークといった表面硬化処理により、この傾向は顕著になる。下図(a)(b)に塗膜パターン断面における内部応力の解析結果を示している。表面硬化処理がない場合は、(a)の様に基板との界面付近に応力が集中する。特にパターンエッジ部では19MPaの最大引張り応力が生じる。パターン断面内に発生する応力は、全て引張り応力である。パターン上部では、界面の影響を受けず応力は徐々に減少する。界面の応力は界面の結合をせん断するように働くため、これは付着強度低下の原因に十分なっている。(b)はDUV照射を行った場合であり、解析上、パターン外周を固定点としている。パターン断面全域において、未処理の場合に比べ大きい引張り応力が発生している。特にパターンエッジでの最大応力は49MPaになり、(a)の場合の約3倍に相当している。表面硬化処理によって、パターンの内部応力が極端に増加する。
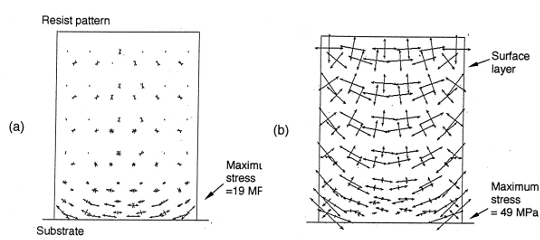
(a)現像後(b)DUV光照射後
DUV照射によって形成される表面硬化層の膜厚は約0.2μmである。この膜厚は塗膜パターンの断面を溶剤に浸し、未硬化層を溶解させた後の観察により求める。DUV照射によってポリマー表面層のクロスリンクが生じ、未照射部よりも密度は高く、逆に熱膨張係数は小さくなる。ここで表面層が付着挙動に及ぼす影響を調べる。下の左図は極端な傾斜を有したパターンの断面SEM写真である。この際、界面部での表面層膜厚は、傾斜のため0.6μmに拡がり、上図(b)の垂直パターンに比べ広くなっている。この表面層下でのHFエッチングによるアンダーカット形状は完全に等方的になる。よって、この表面硬化層における内部応力はかなり低く、そのために付着強度が改善されている。下の右図は塗膜/SiO2界面にHF水溶液がしみ込むメカニズムを示している。上述の様に、パターンエッジ部に応力集中が生じるが、表面硬化層の内部応力はかなり低くなる。よってHF水溶液の界面へのアンダーカットは表面硬化層を過ぎた時点で急激に加速される。その結果、アンダーカット形状は、表面層で等方的になり(図中A)、これを過ぎると異方性的になる (図中B)。よって、図(1)の(b),(c)にある様にアンダーカット形状は2段形状を示す。また、塗膜パターンの全領域がDUV光照射と220℃のベーク処理によって重合された場合、熱応力はかなり増加する。その結果、表面硬化層とパターン内部との境界はなくなり、図(1)の(d)のように2段形状は消滅し、大きいアンダーカット形状を形成する。
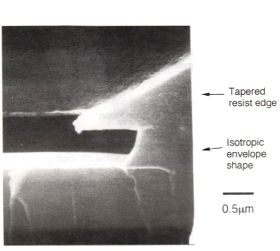
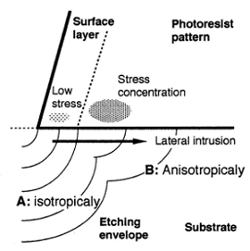
ここで、下の左図は塗膜/基板界面方向に沿った引張り応力分布を示している。横軸の「0」の位置は塗膜表面を示している。(ここで表面層は省略している) 引張り応力は表面で最大となり、塗膜内部になるに従い急激に減少していく。この傾向はDUV照射、及びベーク処理によって加速される。また、パターン線幅の増加と共に応力も大きくなる。ここで、ボトムエッジ部での最大応力とパターン線幅との相関を下の右図に示している。この最大応力は線幅の増加と共に増加し、やがて飽和する。また、この傾向は硬化処理によって顕著になる。この結果は図(2)のアンダーカット量の線幅依存性と似ている。下の右図で変曲点Aは有限要素解析では約3μmの線幅で生じているが、図(2)の実際の付着現象では5~10μmの線幅で生じている。これはヤング率,ポアソン比,熱膨張係数等の解析パラメータが、実際の塗膜材料のものと異なるためである。HF水溶液中での塗膜パターンの付着要因は、塗膜/基板界面上の応力分布に依存することが分かる。
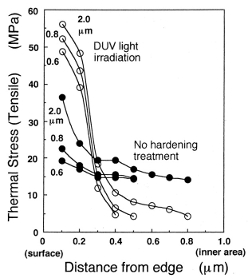
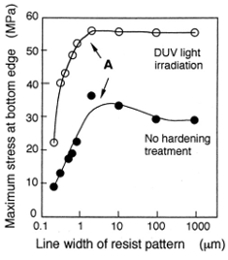
パターン線幅との相関
塗膜/基板界面に生じる応力分布とHF溶液中での付着挙動(アンダーカット)との相関を解析し、その有効性を確認した。塗膜の表面硬化層の形成がアンダーカット形状に強く影響することを確認した。界面付着性コントロールに応力分布制御が有効であることを示した。
参考文献
- Akira Kawai, "Shrinkage Effect of Local Area of Polymer Film on Adhesion Behavior", Jpn. J. Appl. Phys. 33, L973-L974 (1994).
- Akira Kawai,"Adhesion of Micro Window Pattern Formed by Photolithography" J. Adhesion Society of Japan, 31, 360-362, (1995).
- 河合 晃、"レジスト微細パターン内の熱応力分布と接着特性"
- Akira Kawai, "Dependency of Adhesion Behavior on Thermal Stress Distribution in Photoresist Micropatterns", Jpn. J. Appl. Phys. 32, 1020-1024 (1993).
CVD膜の被覆性およびボイド形成
薄膜のコーティング法の一つに化学的気相堆積法(Chemical vapor deposition : CVD)がある。この手法は他のコーティング法に比べて、均一で平坦性に優れている。堆積できる膜も、有機、無機、金属膜となり広範囲である。均一性の観点では、真空チャンバーを用いた減圧CVD法が有効であるが、最近では、大気圧下で行う大気圧CVDも注目されている。ここでは、プラズマを用いたCVD法について述べる。プラズマCVD法では、熱処理などの高温で得られていた膜を低温で形成することが可能となる。ここでは、樹脂材料で形成された周期パターン上へ、HMDS(hexamethyldisilazane, C6H19NSi2 )をソースとして、HMDSO(hexamethyldisiloxane, C6H18OSi2)重合膜をプラズマCVD法により堆積した。パターン周期は0.39~1.5μmの範囲で変化させている。断面形状の観察を行って、重合膜の平坦性を評価する。平坦性の指数として、基板から重合膜表面までの高さについて、各周期パターンの凹部と凸部の比を用いた。パターン周期が約0.75μmになると平坦性の閾値があり、閾値以上のパターン周期では平坦性指数は約0.5と低下する。また、閾値以下では良好な平坦性となるが、重合膜中にボイドが形成される。重合膜中のボイドの形成メカニズムについても述べる。
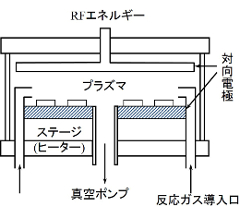
プラズマCVDは減圧で行うため、真空チャンバー、RF高周波電源等の設備が必要となる。右図には基本的な装置構造を示している。真空チャンバー内には、対向電極構造の放電ステージが存在する。ステージは加熱機構がついており、重合反応の促進が可能となる。電極間に13.56MHzの高周波を印加することによりプラズマを生じさせる。キャリアガスとして、通常Arガスが用いられる。液体ソースは減圧により蒸気となり反応室まで送り込まれる。プラズマ重合による反応生成物は、ステージ上の基板に堆積する。
周期パターンとして、ArFエキシマレーザー(波長193nm)に感度を有する化学増幅型レジストを用いた。レジストの主成分はスチレン系の樹脂である。周期パターンの作製プロセスは、以下の通りである。まず、平坦基板上にレジスト膜をスピンコート法により形成した。レジスト膜厚は0.36μmである。そして、ソフトベークを130℃で90秒間行った後で、ArFエキシマレーザを用いて、周期ラインパターンをレジスト膜に露光した。露光量は46mJ/cm2である。そして、熱処理を130℃で90秒間施した後で、パターン現像を行った。現像液は、2.38%のTMAH (tetramethylammoniumhydroxide) 水溶液を使用した。パターン寸法および断面形状は、走査型電子顕微鏡を用いて測定した。下の左図(a)に、パターン断面の模式図を示している。ここで、寸法Aはパターン線幅であり、0.21~0.75μmの範囲で変化させている。また、寸法Bはパターン間隔であり、0.18~0.75μmに変化させた。寸法Cはパターン高さであり0.36μmである。寸法Dはパターン周期であり、0.39~1.5μmの範囲で変化させた。全ての試料において、パターン線幅Aとパターン間隔Bとの比(A/B)が約0.8になるように形成した。
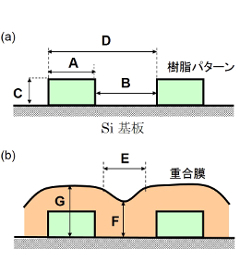
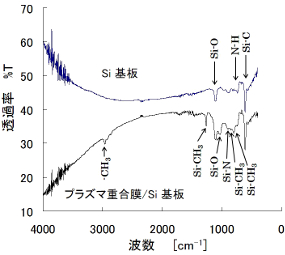
プラズマCVD装置として、サムコインターナショナル社製のPLAMA TOTAL DRY SYSTEM (PDM-303)を使用している。チャンバーは石英製であり、直径250cmの円筒形である。チャンバー内部には、SUS製の平行平板電極が4cmの間隔で容量結合型に設置されている。重合膜のソースとしては、HMDS(nacalai tesque, SPグレード)を使用している。フラスコ内で発生させたHMDS蒸気を、70℃に加熱された配管を通して重合チャンバー内へ導入した。そして、上部電極に設けられた多数の微細孔から、HMDS蒸気がチャンバー内へ供給される。キャリアガスは99.9%純度のArガスであり流量は32sccmである。試料は下部電極の中央部に配置した。RFプラズマの電力密度は、0.16W/cm2であり、放電時の真空度は9Paであった。最終的に、プラズマ重合膜の堆積レートは61nm/minであった。重合膜の構造解析は、フーリエ赤外分光器(FT/IR-410, 日本分光(株))を用いて行う。
上の左図(b)は、重合膜を堆積した後の試料断面の模式図を示している。SEMによる断面形状の観察から、上の左図(a)で定義された各寸法を読み取る。ここで、寸法Eは重合膜表面に生じた窪み幅を示している。この窪み幅は、重合膜の平坦性のパターン周期依存性を感度良く反映する。また、寸法FとGは、それぞれ、パターン凹部とパターン凸部における、基板から重合膜表面までの高さを示している。そこで、平坦性を定量的に解析するために、平坦性指数Pを下式のように定義する。
P = F / G
ここで、P=1は完全に平坦化された状態であり、この値に近いほど良好な平坦性となる。上の右図に重合膜のFT/IR測定結果を示す。ここで、797, 1261 cm-1には、Si-CH3結合に帰属する吸収ピークが確認できる。また、1030cm-1での吸収ピークは、Si-O結合を示している。しかしながら、重合膜のソースであるHMDSを表すN-H結合に帰属する吸収ピーク(739, 3350 cm-1)は検出されていない。よって、堆積された重合膜には、Si-CH3結合とSi-O結合が多く存在していることから、分子構造はHMDSOであると考えられる。
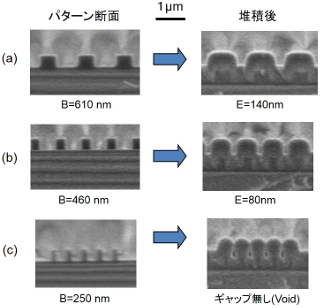
右図(a),(b),(c)に、重合膜の堆積前後での試料断面のSEM写真を示す。パターン周期Dが比較的長い場合は、重合膜はパターン形状に忠実に堆積されていることが分かる。よって、重合膜表面の窪みも深くなり、平坦性も悪くなっている。しかしながら、右図(c)のように、周期Dが短くなると窪みが消滅し、重合膜表面はかなり平坦化されているのが分かる。これらのSEM写真から、上の左図(b)で定義された各寸法(E, F, G)を読み取り平坦性を評価する。そこで、下の左図に、窪み幅Eおよび平坦化指数Pのパターン周期D依存性を示す。各測定値は、試料4個分の平均値と標準偏差を示している。まず、下の左図(a)のように、パターン周期Dの減少に伴って、窪み幅Eも減少することが分かる。すなわち、パターン間への重合膜の堆積が進んでいることが分かる。そして、パターン周期が約0.75において、窪みが急に消滅する閾値が存在している。一方、下の左図(b)に示すように、平坦化指数Pについても、パターン周期Dが0.75μmの時に閾値が存在している。閾値より長い周期では、平坦性指数は約0.5となる。そして、パターン周期Dが0.75μm以下になると、平坦性指数が急激に向上し0.95になることが分かる。
ここで、右上図(c)のSEM写真にあるように、閾値以下の平坦性の良好な重合膜の場合、重合膜中に小さいボイドが形成されている。そこで、下の右図(a),(b)にあるように、重合膜の堆積中にボイドが形成されるメカニズムを考察する。まず、下の右図(a)のように、チャンバー内で合成された重合分子は、堆積中にパターン角部への衝突確率が高くなり、オーバーハング形状が形成される。そして、オーバーハングの存在により、パターン底部での重合膜の堆積が妨げられる。さらに、重合膜の堆積が進むにつれて、最終的には下の右図(b)のように、オーバーハング同士が接触してパターン間にボイドが形成される。すなわち、パターン周期が短いほど、あるいは、重合膜を厚く堆積することにより、ボイドは形成されやすくなる。よって、下の左図のような平坦性の閾値は、ボイドが形成されるパターン周期を示している。ボイド形成を防ぐには、ECR(electron cyclotron resonance)プラズマCVD法などにより、堆積する重合分子の指向性を高くして、パターン角部でのオーバーハング形状の形成を抑制することが効果的である。
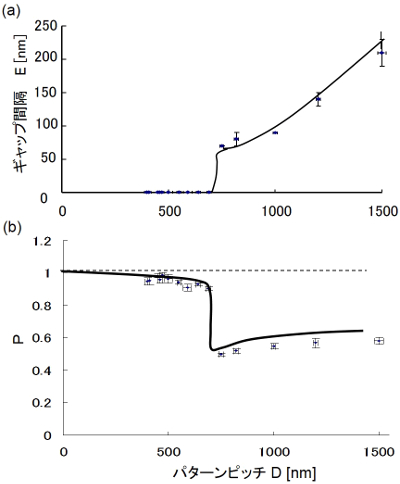
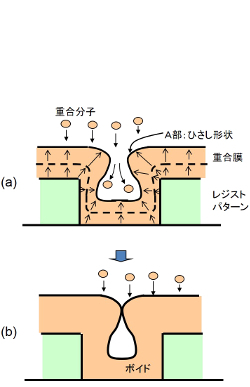
ここでは、周期パターンを用いて、プラズマCVD法により重合膜を堆積した場合の平坦性評価について述べた。平坦性が変化する閾値が、パターン周期に存在することが分かる。この閾値は、重合膜中にボイドが形成される時点を示しており、閾値以下の平坦な膜にはボイドが形成される。堆積初期のオーバーハング形状の形成が、ボイド形成の主要である。また、クラスター核形成の理論により、凸部には重合膜の堆積が促進されることを示した。プラズマCVD法は工業的に重要な成膜方法であり、均一なプロセスコントロールが必要となる。
参考文献
- 河合 晃, "微細周期パターン上へのプラズマ重合膜の堆積特性", 日本接着学会誌, 37, 433-436 (2001).
- Akira Kawai, "Nano-wetting of DI-water analyzed by AFM", J. Photopolymer Science and Technology, 20, 813-814 (2007).
減圧乾燥による内部応力コントロール
乾燥装置における熱量の伝熱メカニズムは、熱風やガスによる対流、加熱板に接することによる伝導、および赤外線や太陽光による輻射に区分される。これらの伝熱メカニズムを効果的に利用する目的で乾燥装置は構成される。また、乾燥装置には、十分な乾燥能力だけでなく、高品位な乾燥プロセスが求められる。近年では、処理基板の大型化が進み、処理能力の向上も望まれている。一方、乾燥装置には、圧力や温度を制御し、過熱やラプラス力による塗膜の劣化を抑える方式も実用化されている。また、大型チャンバーの有無や、乾燥の均一性なども重要な性能である。よって、製品に適した乾燥装置の選択が必要となる。ここでは、代表的な乾燥装置として、加熱乾燥、赤外線乾燥、減圧(真空)乾燥、凍結乾燥、超臨界乾燥に注目し、乾燥機構と装置構成を紹介する。特に、工業上で重要であaる減圧(真空)乾燥後の塗膜の膜質について述べる。乾燥装置により、塗膜は最適な条件で乾燥処理ができる。塗膜と周囲空間との温度差が増大すれば、蒸気圧差が生じ乾燥が促進する。一般に、加熱乾燥の乾燥速度Kは以下のように定義される。
ここで、a:熱伝達係数、Th:熱風温度、Tf:膜温度、q:蒸発潜熱である。乾燥速度を増加させるには、温度差(Th-Tf)だけでなく、熱伝達係数aの向上が効果的であり、これが乾燥装置の設計指針となる。下の左図は市販の加熱型の乾燥装置の外観写真である。用途に応じて、小型から大型まで様々なタイプが市販されている。通常、乾燥装置の最大加熱温度は300℃に設定される場合が多いが、周囲への熱発散を防止するため乾燥室は断熱材で覆われている。断熱材には、ガラスウールなどのファイバー製品が用いられる。金属発熱体には、ニッケル・クロム系、および、鉄・クロム・アルミニウム合金系のものが多用される。電子産業用などの乾燥装置は、塗膜表面への微粒子付着を防止のためフィルタ機構を備えている。下の右図は熱重量測定(TG)により測定した塗工液の乾燥特性を示している。塗工液はノボラック樹脂と溶剤(沸点156℃)の混合液である。加熱温度が溶剤の沸点に近づくにつれ溶剤蒸発が促進される。また、沸点を超えても溶剤蒸発は進み、重量減少が続くことが分かる。
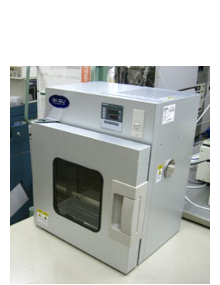
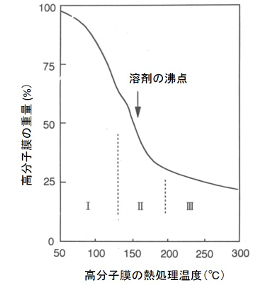
赤外線機器は暖房用として身近であるが、乾燥装置としても広く用いられる。赤外線乾燥では輻射を利用するため大型チャンバーは必要ない。市販のタングステン(W)フィラメントでは、1700~2200℃で放射光の80%が赤外線となる。下の左表は、一般的な赤外線の特徴を示している。遠赤外線と近赤外線は、波長の違いだけでなく、物質内への侵入深さが異なる。近赤外線では、比較的表面層での吸収が高いが、遠赤外線では内部まで侵入し均一な加熱が可能となる。車両塗装後の乾燥などの高品位な用途に用いられる。
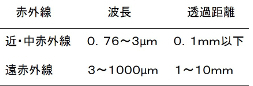
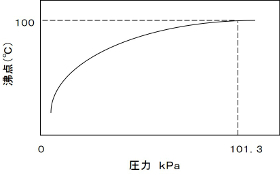
乾燥室内の気圧を下げることで、塗膜の溶剤蒸発を促進できる。液体の沸点は、上の右図のように圧力に応じて下がる。近年では、減圧乾燥は液晶パネルなどの大型基板の塗膜乾燥に用いられる。比較的低温で乾燥が可能なため、耐熱性の低い塗膜の乾燥に適している。しかし、加熱乾燥と異なり急速に乾燥が進むため、塗膜内の歪み発生や微細構造の破壊に注意が必要である。
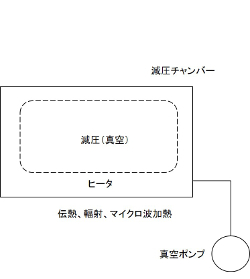
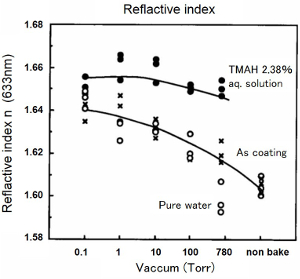
また、内部応力も発生しやすいため、塗膜の耐久性に影響を及ぼす恐れがある。また、バイオや生体試料の乾燥には、組織を破壊するケースが多い。減圧乾燥では、上の左図のように減圧用のチャンバーが必要となるが、蒸気圧差を高く設定できるため、高い乾燥速度を有する。減圧機構として真空ポンプや簡易型のアスピレータ等を用いるが、真空装置のような強固なチャンバーは必要とせず、開閉式の密閉機構で対応できる。しかし、加熱乾燥とは異なり、急速な乾燥であるため塗膜の凝集構造に影響を及ぼす。上の右図は減圧処理および溶液浸漬による高分子塗膜の屈折率変化を示している。減圧乾燥により、塗膜の屈折率が増加する。屈折率は固体の凝集性や分極性を敏感に反映する。よって、屈折率の増加は、溶剤蒸発による塗膜の密度増加を意味する。また、アルカリ水溶液への浸漬により、屈折率はさらに増加する。しかし、純水への浸漬では屈折率は変化しない。
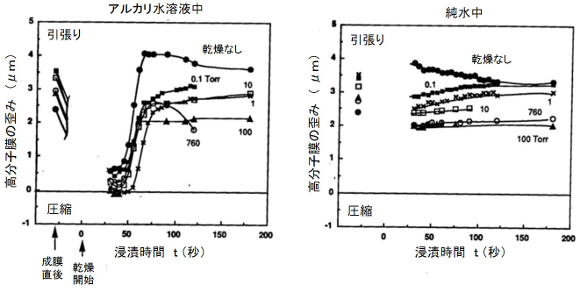
上図は減圧乾燥した高分子膜について、アルカリ水溶液と純水に浸漬後に発生した膜歪みを示している。塗膜の成膜直後には引張り歪みが生じている。しかし、アルカリ水溶液に浸漬後に引張り歪みは緩和され、乾燥時に再び増加する様子が分かる。このような急激な変化は塗膜と基板界面に歪みを生じ、付着性などに影響を及ぼす。しかし、純水に浸漬した場合は、膜歪みの変化は見られず、乾燥後も殆ど変化がない。これは、下図の高分子構造モデルにように、高分子樹脂とアルカリ水溶液との分子間相互作用により、浸透が促進されるためである。また、乾燥が不十分で残留溶剤が多いほど、アルカリ分子の浸透は速くなり膜歪みを生じる。また、水分子は分極率が高いため、高分子構造への浸透性が低くなると考えられる。
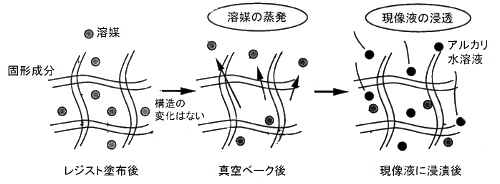
ここでは、代表的な塗膜の乾燥装置について、装置機構および特徴について述べた。試料の大型化だけでなく、高品位な乾燥プロセスの要求が高くなり、乾燥装置の絶え間ない進展がみられる。塗膜の高品質化には、塗膜の性質に適した乾燥装置の選択が重要となる。
参考文献
- Akira Kawai, "Characteristics of Adhesion between Photoresist and Inorganic Substrate", Jpn. J. Appl. Phys. 28, 2137-2141 (1989).
- Akira Kawai, "Adhesion of Resist Micropatterns during Drying after Water Rinse", Jpn. J. Appl. Phys., 34, L1093-L1094 (1995).
屈折率による膜の浸透・膨潤解析
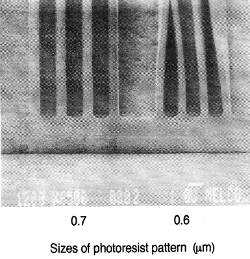
軟化・膨潤
物質の凝集性は、固体および液体として機能性を発現させるために重要な物性である。凝集性を表す物理量には、硬さ、硬度、粘性、分子量分布、ヤング率、応力、歪み、塑性、脆性、摩擦、摩耗などのように多種多様である。その殆どは、荷重印加や熱などの外部刺激に対する応答として測定するため、一種の破壊試験に位置づけられる。最近では、ソフトマターのような凝集性の弱い新材料分野が注目されており、これらは機械的試験法では解析しにくい。一般に、高分子材料は無機金属材料とは異なり、その構造内にナノスケールの空間を有している。よって、高分子膜内には、水分や気体などが容易に浸透し、膨潤や収縮が生じる。右図はアルカリ水溶液中に浸漬した高分子パターンの膨潤・軟化による変形を示している。このような凝集性の低い材料の場合は、屈折率を用いた手法が適している。屈折率は光学材料や分光分析の分野で重要な物理量であるが、その値には材料の凝集性が反映されている。また、屈折率の測定は、一般的に非破壊で行えるため、ソフトマターや微小試料にも有効である。
下の右図はノボラック樹脂をベースとした高分子膜に対して、絶対膜厚(触診式)と屈折率(エリプソメーター)の測定結果を示している。この場合、アルカリ水溶液に浸漬させた時間を横軸に示している。浸漬時間の増加に伴い膜厚が増加することから、アルカリ水溶液が高分子膜中へ浸透し、膜の膨潤が生じたと考えられる。また、屈折率は浸漬時間に伴い減少していることが分かる。
一般に、屈折率nと物質の凝集性との関係は、以下のクラウジウス・モソティの式で表される。
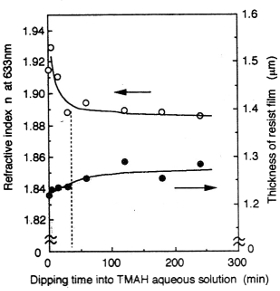
浸漬時間依存性
ここで、εは誘電率、Nは分子数密度であり、αは分子分極率である。分子構造が大きく変化しない場合、分子分極率αは一定として扱う。すなわち、この式に基づけば、屈折率変化は分子数密度の増減をそのまま反映することとなる。よって、右図の高分子膜の屈折率低下は、アルカリ水溶液の浸透と膨潤によって、分子数密度が低下し膨潤が生じたことを示唆している。このように、屈折率測定によって、非接触で高感度に材料の凝集性を解析できる。屈折率は、エリプソメーター、アッベ屈折計、光干渉法など用いて容易に測定できる。また、薄膜、バルク、溶液などの様々な試料状態で測定可能である。
参考文献
- Akira Kawai et.al, "Adhesion between Photoresist and Inorganic Substrate", Jpn. J. Appl. Phys. 30, 121-125 (1991).
- 河合 晃 他, "フォトレジスト膜へのアルカリ水溶液の浸透と接着性", 日本接着学会誌, 32, 294-297 (1996).
- Akira Kawai, "Cohesion property of resist micro pattern analyzed by using atomic force microscope (AFM)", J. Photopolymer Sci. Technol, 16, 381-386 (2003).